Flexible plastic extrusion profiles and custom plastic extrusion parts have revolutionized the way we approach product manufacturing and design. The versatility and adaptability of these materials have made them an essential component in various industries, from automotive to consumer goods. Here's a closer look at how flexible plastic extrusion profiles serve various industries and why their customizability is key to innovation.
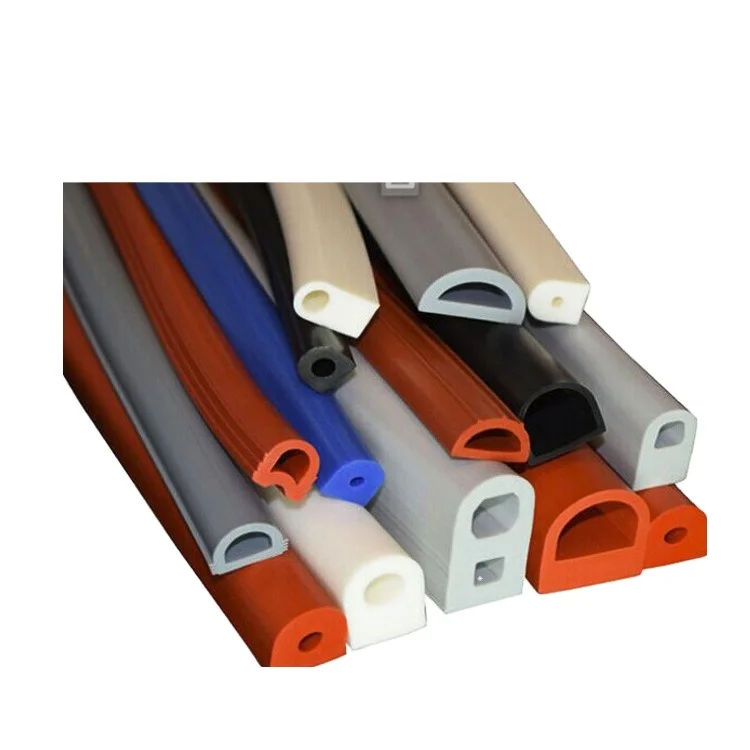
Flexible plastic extrusion profiles offer unique solutions across many sectors, allowing manufacturers to create components that can bend without breaking while maintaining structural integrity. This flexibility is particularly valued in industries where space constraints and dynamic environmental conditions challenge conventional materials. These profiles can be designed to suit specific applications, such as creating seals, insulation, and even complex geometrical paths, providing a perfect blend of durability and usability.
Take the automotive industry, for example. Here, flexible plastic extrusion profiles are invaluable for producing components that require resilience and adaptability, such as interior trims, bumper cushioning, and door seals. The need for vehicles to withstand varying weather conditions and mechanical stresses makes flexible plastics an ideal choice. Custom plastic extrusion parts ensure that every component fits precisely, improving performance and safety for end-users.
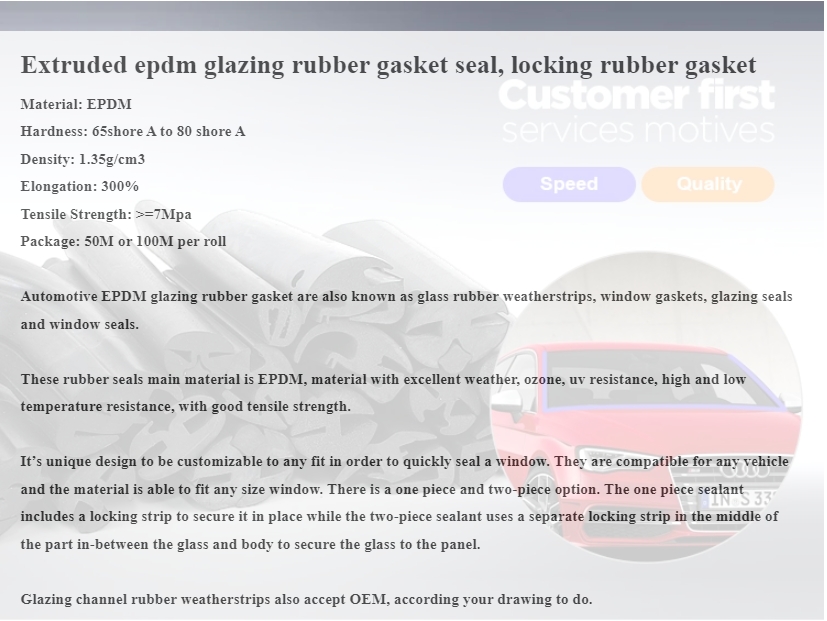
In construction, the importance of custom extrusion profiles cannot be overstated. They allow for the seamless integration of components into larger structures, enhancing structural integrity while minimizing waste. Flexible plastics can be shaped into complex profiles that can serve as weather-proofing solutions, window trims, and cable management systems. These custom profiles help to create more efficient buildings, optimizing energy use and ensuring longevity.
Moreover, flexible plastic extrusion is pivotal in the consumer goods sector. The demand for aesthetically pleasing yet functional designs necessitates a material that can be both flexible and durable. From the manufacturing of household appliances to gadgets, custom plastic extrusion parts enable manufacturers to innovate rapidly without compromising on quality. The ability to tailor designs to specific requirements has pushed the boundaries of product development, allowing devices to be lighter, more efficient, and sustainable.
flexible plastic extrusion profile custom plastic extrusion parts
Innovations in medical devices also rely heavily on flexible plastic extrusion. In this field, precision and reliability can be a matter of life and death. Custom plastic parts are used extensively, from tubing and catheters to enclosures for sensitive medical equipment. The flexibility of plastics ensures that components can adapt to the human body's contours, providing comfort and enhancing functionality. Furthermore, the hygiene standards achievable with plastics make them indispensable in medical applications.
For those in the supply chain and logistics management, flexible plastic extrusion profiles provide practical applications as well. They can be used to design impact-resistant packaging and containers, which are essential for the safe transport of goods. Custom parts can reduce shipping costs by optimizing space and providing tailored protective solutions for fragile items. Such innovations ensure products reach their destinations in perfect condition, minimizing loss and waste.
Digitizing the manufacturing process through extrusion technology also enhances the capability to produce these custom parts efficiently. Advances in technology, such as 3D printing, enable manufacturers to design and test prototypes quickly, accelerating the overall development cycle. This capability ensures that products meet user requirements without extensive delays or increased costs.
An additional aspect of flexible plastic extrusion profiles is their contribution to environmental sustainability. Many custom parts are now developed using biodegradable materials, reducing their environmental footprint. The recyclability and reusability of plastic components mean they can be reformed into new products, promoting a circular economy. This environmentally friendly approach resonates well with both manufacturers and consumers seeking green alternatives.
In the competitive landscape of modern industry, leveraging flexible plastic extrusion profiles and custom parts is not merely beneficial but necessary for companies aiming to stay ahead. Their adaptability allows businesses to innovate continually, offering products that not only meet but exceed customer expectations. Engaging with materials and technologies that reflect the ideals of Experience, Expertise, Authoritativeness, and Trustworthiness ensures that companies maintain a stronghold in their respective markets, fostering trust and excellence that stands the test of time.