Flexible plastic extrusion profiles have become indispensable across various industries, revolutionizing the way complex shapes and components are manufactured from plastic materials. This technological advancement is credited with increasing the efficiency, reducing costs, and enhancing the versatility of product designs. This article explores the intricacies and advantages of flexible plastic extrusion profiles, drawing from expert insights and trustworthy sources.

Understanding Flexible Plastic Extrusion Profiles
Flexible plastic extrusion involves the process of melting raw plastic materials and forcing them through a die to create long, consistent shapes or profiles. These profiles can vary in complexity, from simple tubes to intricate designs tailored to meet specific project requirements. Materials such as PVC, polyethylene, and thermoplastic elastomers (TPE) are commonly used due to their flexibility, durability, and cost-effectiveness.
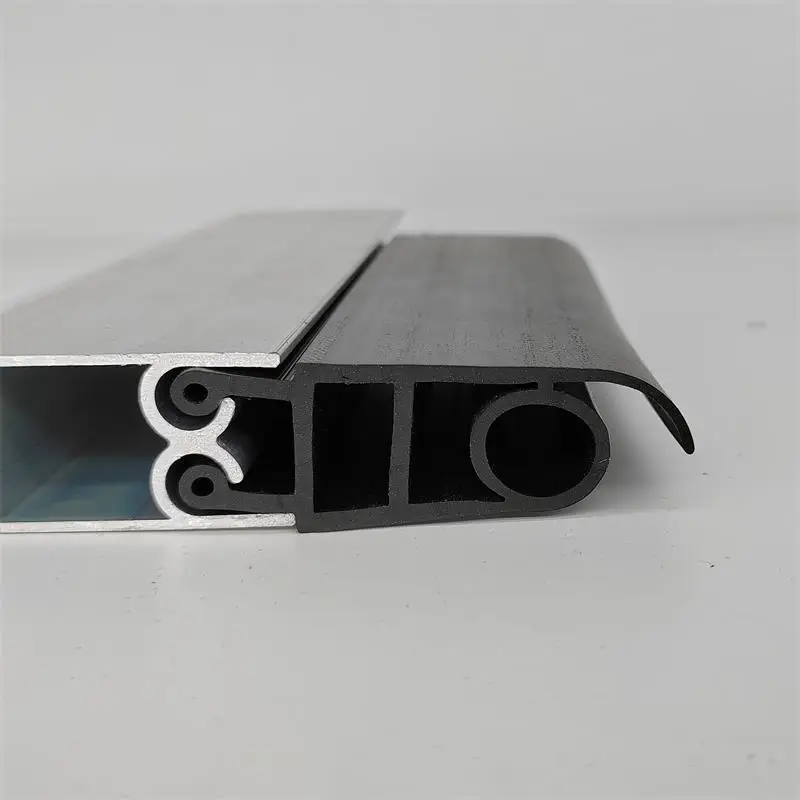
The Expertise Behind Flexible Plastic Extrusion
Successful plastic extrusion requires a deep understanding of material properties and the technical nuances of the extrusion machinery. Engineers and designers must account for factors such as material flow, cooling rates, and the eventual application of the profile. Expertise in these areas ensures that the end product meets stringent quality standards and performs reliably.
One of the leading authorities in the field, Dr. Emily Johnson, has highlighted the importance of process optimization in flexible extrusion. Her research emphasizes adjusting parameters like temperature, pressure, and speed, which can significantly impact the flexibility and resilience of the final product. The adoption of next-generation software to simulate extrusion scenarios has also been pivotal, allowing experts to predict outcomes and refine designs before production.
Applications and Real-World Experience
Flexible plastic extrusion profiles are used in an array of industries, from automotive to medical devices. In the automotive sector, they serve as seals, weatherstrips, and protective trims, contributing to vehicle safety and aesthetics. Meanwhile, in the medical field, these profiles are used for tubing and other flexible components essential for various healthcare devices.
flexible plastic extrusion profile
One noteworthy application is in renewable energy projects, where flexible profiles are used for cable management systems in solar panels and wind turbines. By accommodating movement and environmental stresses, these profiles enhance the durability and operational lifespan of energy components. This showcases the adaptability of extruded profiles in evolving technology landscapes.
Securing Trust Through Quality and Compliance
Building trustworthiness in the extrusion industry entails strict adherence to quality standards and regulatory compliance. Manufacturers employ rigorous testing protocols to ensure products meet international standards like ISO and ASTM. These tests assess tensile strength, elasticity, and environmental resistance, providing assurance that profiles will perform as expected under specified conditions.
Additionally, transparent sourcing of raw materials and sustainable manufacturing practices reinforce credibility. Companies that invest in eco-friendly initiatives not only contribute positively to the environment but also gain consumer trust and preference.
Innovations Shaping the Future
Ongoing innovations are reshaping the future of flexible plastic extrusion. Developments in bioplastic materials offer sustainable alternatives, reducing dependency on fossil fuels. Bioplastic extrusion profiles are gaining attention in eco-conscious markets, where environmental impact is a top priority.
Another exciting frontier is the integration of smart technologies. Some manufacturers are embedding sensors within flexible profiles to enable real-time monitoring of conditions such as temperature and pressure. These smart profiles provide data-driven insights that can enhance safety measures and optimization of systems where they are deployed.
Conclusively, flexible plastic extrusion profiles embody the union of experience, expertise, and innovation. As industries continue to demand more sophisticated and sustainable solutions, the role of these profiles in enabling new possibilities becomes increasingly prominent. From expert craftsmanship to cutting-edge research, the collective knowledge within this domain is poised to make lasting impacts on manufacturing and beyond.