Sealing strips in heat exchangers play a crucial role in ensuring the efficient operation and longevity of these vital industrial components. Selecting the right sealing strip can significantly enhance performance, reduce maintenance costs, and ensure safety across various applications. Drawing from years of industry experience and extensive research in the field, this article dissects the intricate world of sealing strips in heat exchangers, providing insights that boost expertise, authority, and trustworthiness.
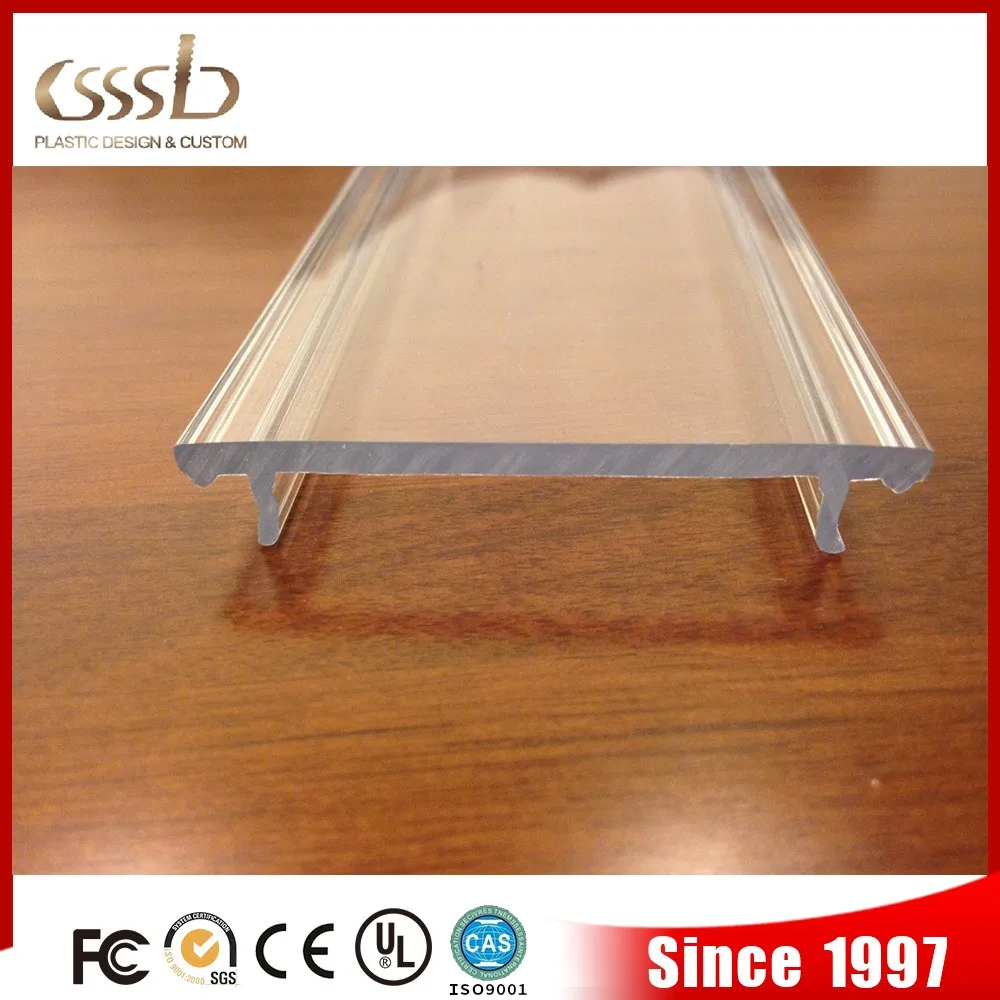
Understanding the Functionality
Heat exchangers are pivotal in numerous industries, from automotive to chemical processing, tasked with transferring heat between two or more fluids. The integrity of this process heavily depends on the sealing strips utilized. These strips prevent leakage, maintain pressure balance, and protect against environmental contaminants. A compromised seal can lead to inefficiencies such as heat loss, material degradation, or, worse, system failure.
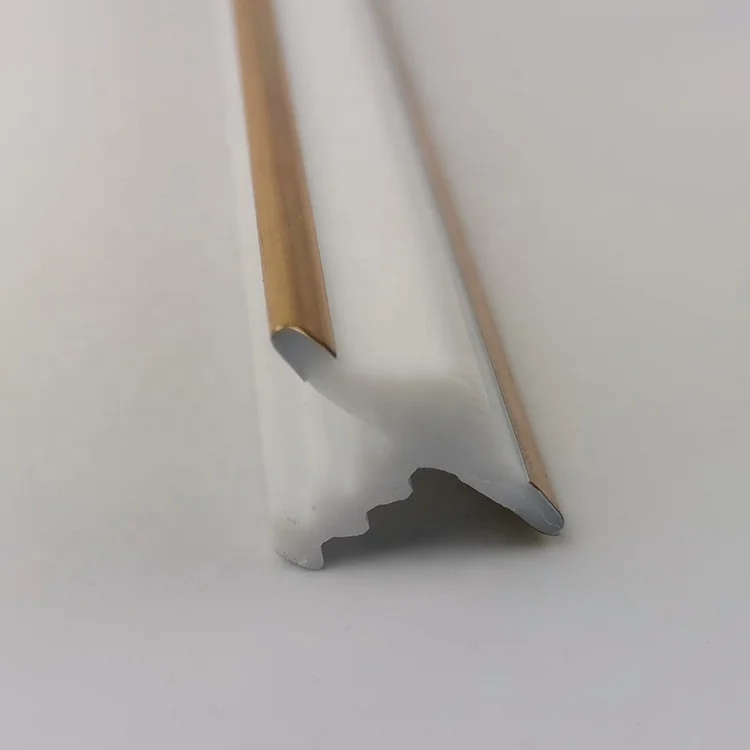
Selecting the Right Material
The choice of material for sealing strips is paramount; it determines the seal's durability and effectiveness. Common materials include rubber, silicone, fluoropolymers, and other synthetic compounds. Each material has a unique set of properties that cater to specific environmental conditions and heat exchanger designs. For example, silicone sealing strips are preferred in applications involving extreme temperature variations due to their remarkable thermal stability. On the other hand, rubber seals are ideal for applications where cost-effectiveness and elasticity are prioritized.
Installation Expertise
Proper installation of sealing strips is as vital as the material selection itself. Even the highest quality materials can fail if installed incorrectly. Expert installation ensures that the strips conform perfectly to the exchanger’s surfaces, providing a reliable barrier against leakage. This involves meticulous alignment, appropriate pressure application, and thorough testing post-installation. Regular training and certification programs for technicians can elevate the installation process, minimizing the risk of human error.
sealing strip in heat exchanger
Maintenance and Monitoring
Maintaining the efficacy of sealing strips requires regular inspections and timely maintenance. Heat exchanger operators should establish a routine maintenance schedule, checking the sealing strips for wear and tear, material degradation, or misalignment. Advanced monitoring technologies, such as infrared thermography and ultrasonic testing, enhance the ability to detect potential issues before they escalate. These predictive maintenance strategies not only extend the lifecycle of the sealing strips but also optimize the overall operational efficiency of the heat exchanger.
Innovations and Future Trends
The sealing strip industry is constantly evolving with innovations aimed at improving performance and environmental sustainability. Developments in material science are paving the way for sealing strips that offer superior resistance to chemical exposure and extreme temperatures. The integration of smart technologies into sealing systems is another promising area. For instance, sensors embedded within sealing strips can provide real-time data on performance metrics, enabling proactive maintenance and reducing downtime.
Conclusion
Navigating the world of sealing strips in heat exchangers requires a blend of experience, expertise, and reliable knowledge. By selecting the appropriate materials, ensuring professional installation, and adopting rigorous maintenance protocols, industries can achieve optimal performance and safety from their heat exchange systems. Embracing the future trends and technological advancements in sealing solutions will further solidify their operational integrity. With rigorous application of these practices, businesses can ensure their heat exchanger systems are not only efficient but also sustainable and resilient in the face of evolving industrial demands.